DfMA Wales
Unlocking the potential of Design for Manufacture and Assembly (DfMA) would present a paradigm shift in the construction sectors ability to support a green, prosperous and equitable Wales.
DfMA Wales
DfMA Wales is a private sector led consortium, of which CEWales is a founder member, that has united to focus on the advantages of DfMA to Wales, as a key enabler to a more efficient construction industry. DfMA Wales ambitions are to “Foster greater collaboration in Construction between Government, Industry, and Academia in Wales to deliver sustainable prosperity for our regions and communities” by recognising the significant sector performance and enhancement possible through mainstreaming the use of DfMA.
Why DfMA
“Currently, the UK’s construction industry is not living up to its full potential. It contributed £117 billion to the UK economy in 2018 and supports over two million jobs, but is one of the nation’s least productive industries, and the built environment is a major contributor to greenhouse gas emissions. The government can use its weight as a major construction client to transform and modernise the industry.”
Source: National Infrastructure Strategy, HM Treasury. Nov 2020
The Construction Playbook lays out best practices and sector reforms that will create a more effective construction industry and describes Modern Methods of Construction (MMC) as a route to transforming how we deliver public works projects. MMC is a wide term covering a range of offsite manufacturing and onsite techniques, providing alternatives to traditional delivery with significant improvements in productivity, efficiency, and quality. If MMC has been set as the goal and defines ‘what we are seeking’, then DfMA is the process that describes ‘how it is done’.
Making the Case for DfMA in Wales
As governments seek to ramp up infrastructure spending, the construction sector needs to address the challenges of delivery in half the time, with half the carbon, and for two-thirds of the cost, whilst also addressing skills shortages and enhancing project and social outcomes. This cannot be achieved by ‘tweaking’ the way that we currently work, the only way is to do things differently. The way to break this cycle of inefficiency is to concentrate on process. We must do things differently and improve our practices. DfMA Wales believes the answers to these challenges rest within the transformative processes of DfMA and all it enables. If Wales can get the strategy right, we should be able to deliver more as an industry, so Wales PLC will benefit considerably. Deployment of the process should also be simpler: assembly should be highly methodical and well universally understood. With a platform design and a standard kit of parts, upgrades, replacement, and renewal become quicker and more straightforward. We move from continuous reinvention to repeatability & continuous improvement.
The Wales DfMA Programme
DfMA Wales will champion this industry transformation through an ongoing series of surveys, meetings, workshops, events, blogs, reports, projects, case studies, exemplars and evidenced examples of best practice to inspire every part of the industry’s supply chain. Constructing Excellence in Wales, as the united voice of the Welsh built environment sector, will host news and articles here for all to share.
A case in point – the Dragon's Heart hospital in Cardiff
DfMA enabled the delivery of the Dragon's Heart Covid-19 surge hospital within the Principality Stadium at record pace at a time of national emergency. Building one of Europe's largest tented structures under the stadium's closed roof and constructing large raised platforms over the lower stands created the space for the new ward infrastructure on and around the pitch. The many small and odd shaped spaces and large temporary structures added technical and design complexity to the base logistics of building a massive hospital in a matter of weeks, but DfMA processes facilitated the works with the first beds available within just 10 days. A remarkable result epitomising the potential of both collaboration and DfMA to transform the construction sector’s day to day performance in normal times.
DfMA Wales - First Industry Survey
Chief Executive Cat Griffiths-Williams sets out initial findings from the CE Wales DfMA Survey.
In early April 2021 we launched our first CE Wales DfMA survey and were delighted to quickly get a representative sample of responses from those on our data base.
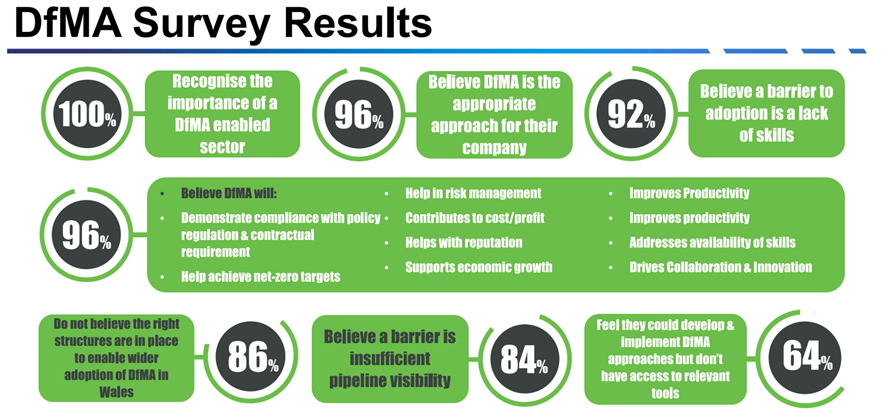
Highlights:
- Lack of awareness
100% of those surveyed have worked on a project that has made use of DfMA, MMC or offsite construction and recognise its importance, however there is still a lack of awareness within the sector of what DfMA is (92%). 80% Don’t think the DfMA processes are well defined and understood.
- Lack of structure, data and training
68% do not believe the right structures are in place to enable DfMA. 80% do not have the right data, metrics, case studies and evidence available to make informed decisions and do not have access to training and guidance to enable DfMA to be implemented. 92% believe a barrier is a lack of skills, 84% believe a barrier is insufficient pipeline visibility.
- Industry ability
64% feel they have the ability to develop and implement DfMA approaches but don’t have access to the relevant DfMA tools.
- DfMA is the right approach
96% believe DfMA is the appropriate approach for their company. Furthermore, the majority of those surveyed (96%) believe DfMA will aid in:
- Demonstrating compliance with policy regulation and contractual requirements
- Helping achieve net-zero targets
- Helping in risk management
- Contributing to cost/profit
- Demonstrating innovation
- Helping with reputation
- Strengthening the sectors support for economic growth
- Improving productivity
- Addressing availability of skills
The survey will soon be re-opened to expand the survey base, and a new survey will also be launched focussed on those clients that procure buildings and infrastructure that have the potential to be DfMA enabled. This will assess their readiness to lead the industrialisation of the sector which would reap significant rewards for the sector in Wales and beyond. More details on what DfMA actually is and those anticipated benefits will be published soon as survey results are assessed.
BLOG: What is Design for Manufacture and Assembly (DfMA) and what is in it for Wales?
Paul C Maliphant, Chair of the Board of Management, CE Wales and Development Director (Wales), Mott MacDonald Ltd seeks the answers.
The Construction Playbook published in December 2020 lays out best practices and sector reforms that will create a more effective construction industry and describes Modern Methods of Construction (MMC) as a route to transforming how we deliver public works projects. MMC is a wide term covering a range of offsite manufacturing and onsite techniques, providing alternatives to traditional delivery with significant improvements in productivity, efficiency, and quality. If MMC has been set as the goal and defines ‘what we are seeking’, then DfMA is the process that describes ‘how it is done’.
DfMA is a collaborative design approach, a process that makes things easy to make and easy to put together (ideally including commissioning and handover) in addition to meeting in-use requirements. It is agnostic of the way assets are delivered, focusing only on making that delivery process better. It enables offsite construction and makes it more effective, but the two are different things, and just because you have one it does not mean you have the other. This design approach has traditionally been applied to sectors such as automotive to efficiently produce high quality products in large numbers. More recently, construction contractors have started to apply DfMA principles to construction to deliver a step change in efficiency. DfMA holds the key to unlocking the latent talent and the true potential of the Welsh construction and manufacturing industries.
Components are key for DfMA, but it is important that the components are flexible enough either individually or collectively when assembled to deliver the facility flexibility needed to be effective in use. This is one way to ensure interoperability that is a desirable outcome for enabling uptake and use across building types and sectors. One of the attributes of platform DfMA (PDfMA) is the potential for common platforms to serve several typologies and use classes, for example we could use the same component in a school and a hospital. Furthermore, manufacturing of components can be undertaken in community-based manufacturing hubs, bringing work to the workforce rather than to the construction/assembly site. This can address some of the inequalities in construction whilst keeping funds circulating locally supporting the foundational economy and thus maximising the value of the Welsh pound.
Digital ways of working can act as a catalyst for making DfMA a success: digital technology makes it easier for clients to present their requirements to market, and designers, contractors and suppliers can then collaborate and/or compete to develop new solutions around those requirements. As well as producing better outcomes, this process leads to the progressive development of marketable skills for these players in the industry. Furthermore, DfMA supported by digital design platforms will encourage innovations in the way infrastructure is operated and maintained (e.g. through digital twins, and digital asset management) and in delivery models (contributing to higher performing enterprises). If it is a success, desirable products – whether they are components, kits of parts, entire modular assets, or the digital tools that help create them – will be created.
These skills, techniques and products could all represent an export opportunity for a country such as Wales if it can lead the way in developing world-beating DfMA expertise. Conversely, countries that do not invest in their own capabilities may end up needing to import solutions from elsewhere in the world later, at higher cost.
In our next post on DfMA we will look more closely at the better outcomes that a DfMA enabled industry could deliver.
BLOG: Supporting a Green Recovery
Paul C Maliphant, Chair of the Board of Management, CE Wales and Development Director (Wales), Mott MacDonald Ltd outlines the anticipated benefits.
Development of a proactive DfMA plan for Wales would initiate the transition from outdated traditional methods and approaches to construction, to a semi industrialised industry delivering enhanced outcomes that would include:
- Support for a green recovery including diving out waste and associated carbon and achieving net-zero targets.
- Support for an Equitable recovery and the foundational economy.
- Delivery of better quality assets and better outcomes.
- Driving sector innovation.
- Developing world-beating skills, techniques and products.
- Increases in the speed of project and programme delivery.
- Improved sector productivity and reduce capital cost.
- Increasing the predictability of employed capital.
- Strengthening the construction sector’s contribution to economic growth.
This article outlines DfMAs key green credentials.
With governments across the developed world setting themselves ambitious targets for the elimination of carbon emissions, the infrastructure sector will be required to play its part by reducing operational carbon from infrastructure and embodied carbon from new assets.
The UK and Welsh Governments are committed to reducing national carbon emissions to net-zero by 2050. While the UK government has pledged to power every UK household with renewable energy by 2030, it is a lot harder to decarbonise quarrying and mining, cement and steel production, at least in the near term. As the rest of the economy gets greener, construction will proportionally account for an ever-larger share of national emissions unless action is taken. Until zero-carbon materials become a reality, the greatest strides to decarbonise construction will be by cutting the quantities of materials used.
DfMA can help achieve a step change in sector performance, by designing out waste at every stage of the project lifecycle, embedding best practice on energy and resource use into new standards, extending asset life through ease of maintenance and flexibility, and promoting continuous improvement.
With cutting carbon and saving cost closely aligned, the enhanced environmental and economic outcomes of DfMA will together boost the prospects of a ‘green recovery’.
In 2013 the UK government’s Infrastructure Carbon Review (authored by Mott MacDonald) set out a carbon reduction hierarchy. DfMA is high up in that hierarchy.
Wastage of materials and resources is an endemic problem when constructing buildings and infrastructure. Projects are still being delivered where up to half of the materials brought to site are wasted and end up in landfill, not in the finished asset.
As well as adding unnecessary cost, wastage increases the carbon footprint of a project with carbon estimates at the design stage usually falling significantly short of the figure on completion. Carbon arising from producing and transporting materials is known as embodied carbon, so if up to 50% of materials delivered to site go to waste, the embodied carbon footprint will be up to twice as big as calculated at design. Delays associated with traditional construction methods add further to the carbon impact, due to the emissions associated with transport and labour.
Waste arises from:
- Designs that are difficult to build or that ignore standard dimensions and units, resulting in leftover quantities.
- Over-ordering due to caution or uncertainty.
- Transporting and storing unused materials.
- Weather and accidental damage of materials in storage.
- Poor supply chain co-ordination, and
- Human error.
It is not just big infrastructure that is responsible: the issue affects construction projects of all kinds and at every scale.
Reduced wastage and increased efficiency have long been arguments in favour of DfMA, where designs are based on modular, standardised components, built in a factory and then assembled when they arrive on site. But the industry has been slow to adopt these methods, even with an apparently clear financial incentive to do so.
DfMA has the potential to make a transformative difference. Waste is driven out at each stage. Design is optimised for manufacture. Manufacturing is resource efficient. Any waste arising from manufacture is recovered for recycling with the assembly of components becoming the dominant activity of construction sites. Factory-based manufacturing simplifies supply chain logistics, with raw materials being delivered to manufacturing hubs rather than to multiple construction sites. Modules are delivered from factory to site only when needed, using ‘just in time’ principles, so there is reduced risk of wastage resulting from sequencing errors, no stockpiling and over-ordering, and no accidental damage, as the modules are lifted straight into position on delivery.
The above starts to describe the common ground between DfMA and a circular economy for the built environment. Indeed, the transition to a fully circular economy for construction is embedded in the DfMA story (or vice versa!). The circular economy is fundamentally about recovering lost value and resources through systems that are regenerative by design. The infrastructure sector, by virtue of its material intensity, is uniquely situated to drive this green economic transformation.
The circular economy, as traditionally known, is a useful framework for addressing issues around waste management and unlocking opportunities in product design. However, far too much pressure and too high expectations have been deferred to the waste management industry to close the circularity loop in the infrastructure sector. By breaking down the circular notion and applying it holistically across the lifecycle of assets we identify green opportunities at each stage that can be best captured by focussing on making the delivery process better. This is DfMA, capturing value by focussing on innovative alliances between actors working across all stages of an assets life cycle, as well as production methodologies.
Turning DfMA into mainstream practice will make a major contribution to decarbonising construction. But it won’t happen unless infrastructure owners, designers, constructors and the supply chain work together. How to do that is mapped out in the international standard for managing carbon in infrastructure, PAS 2080 (authored by Mott MacDonald), which provides the ability to align the whole supply chain with the net-zero goal.
Now is the time to plan for construction to be a key component of a green recovery – with high-skilled high-paid jobs that offer the extra satisfaction of helping to make our nation cleaner, greener and more beautiful. Making Welsh towns synonymous with green construction technologies and the jobs they bring, DfMA manufacturing methods will support a green construction industry across Wales that helps to secure the future of Welsh construction, accelerates our path to net zero and will lay the foundations for decades of economic growth by delivering low carbon building supply chains. DfMA will directly support delivery of the targets outlined by the ‘Ten Point Plan for a Green Industrial Revolution’ published by HM Government, November 2020.
In our next post on DfMA we will look more closely at the better social outcomes that a DfMA enabled industry could deliver.